- Corporate Overview
- Business sites
- Kambara Complex
Business sites
Kambara Complex
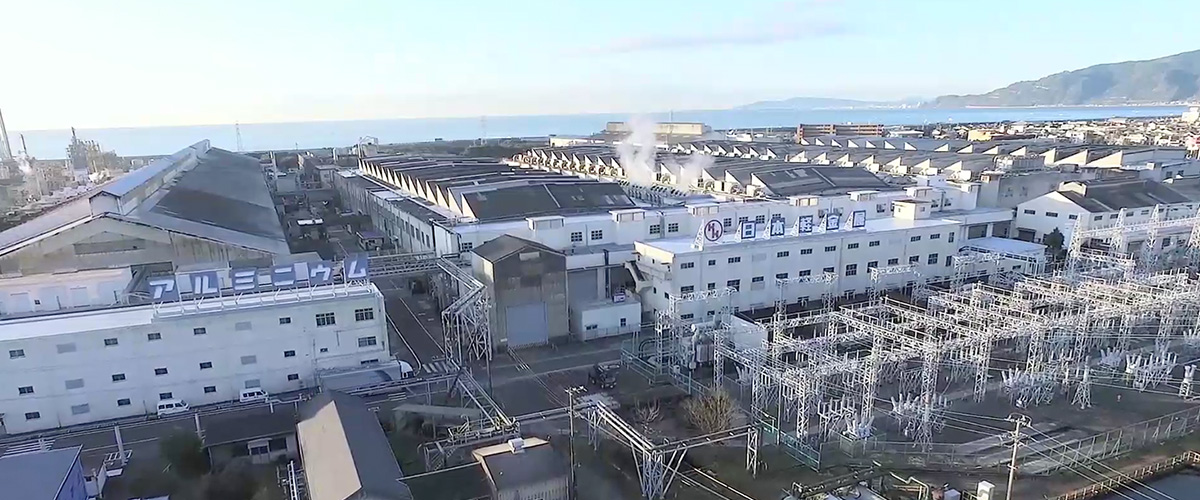
Overview
The Kambara Complex is a composite organization composed of different divisions of Nippon Light Metal Co., Ltd. Specifically, the organization comprises the following facilities and additionally includes plants dedicated to new businesses and the manufacture of products under development:
hydroelectric plants, which supply power to each plant;
the Kambara Casting Plant, which produces 99.99% pure aluminum;
the Kambara Casting Plant (Casting Section), a supply depot for all kinds of materials for aluminum products; and the Extrusion Plant of Nikkei Kambara Co., Ltd., which manufactures various extrusions;
the Kambara Capacitor Foil Plant, which processes anodized foil for electric capacitors with chemicals;
the Kambara Plant of Nikkeikin Aluminum for Mobility Co., Ltd., which manufactures mobility-related products; and the Kambara Chemical Plant, which produces caustic soda and other chemicals.
The neighborhood is also home to Nikkei Research and Development Center, which carries out R&D functions for the NLM Group, and other group companies. Within the NLM Group that defines itself as technology company, the Kambara Complex is responsible for multiple lines of business, from aluminum materials to fabricated products. Taking full advantage of technological expertise accumulated over the years, we will continue to meet the diverse needs of customers as an industrial aluminum complex complete with private hydroelectric plants.
- Site area
459,000m2 - Start of operation
October 1940
Hydroelectric Equipment
The electric power for running the plants in the Kambara Complex are mostly supplied from private hydroelectric plants, with only the shortfall portion being covered by purchased power. Along the middle and downstream parts of the watershed areas of the Fuji River, our private hydroelectric equipment consists of high floodgates at Amahata Dam and Kakimoto Dam; low floodgates at Kuretsubo, Hakiigawa, Shionosawa, and Toshima; headraces; and six power plants with a total output of 144,500 kW. All power plants are monitored and controlled from the control room in the Kambara Complex.
- Production items
Electric power - Equipment and capacity
Fujikawa First Power Plant42,000kW
Fujikawa Second Power Plant49,500kW
Hakii Power Plant21,900kW
Sanogawa Power Plant5,800kW
Motosu Power Plant12,300kW
Sumise Power Plant13,000kW
Kambara Casting Plant
The Casting Section manufactures billets and slabs of every possible kind of composition, quality and shape from all alloys of 1000 series (pure aluminum) to 8000 series to high purity 99.99% aluminum.
For the production of billets, which serve as materials for extrusion and casting, the center is capable of producing a wide variety in small lots. The center is also equipped with homogenization treatment machines powered by a state-of-the-art homogenizing system. For the production of slabs, which serve as materials for sheets and foils, large slab lines and high quality slab lines have been installed to cover a wide range of needs, from slabs for general foils and printing sheets to high tech materials. As ingot supply depot underpinning the broad downstream operations of the NLM Group, the Kambara Casting Plant plays a key role in our technological operations.
- Production items or lines of business
Segregation section
Aluminum ingots
99.98% to 99.9999% (segregation method)
Casting section
Billets (pure aluminum series, alloy series, high purity series)
Slabs (pure aluminum series, alloy series, high purity series) - Equipment and capacity
Segregation section
Segregation method smelting furnace: 7,000 t/year
Casting section
110,000t/year
Extrusion Plant of Nikkei Kambara Co., Ltd.
To set up a production and supply base for aluminum and aluminum alloy extrusions, Nippon Light Metal Co., Ltd established the Extrusion Plant in 1973 at a site adjacent to the Kambara Casting Plant, the supplier of billets used at the new plant as main raw materials. The first extruder started operation in November 1973 at the Extrusion Plant. Initially, the Extrusion Plant focused on the manufacture of extrusions for construction using direct extruders. Faced with increasing demands from the two-wheeled and four-wheeled vehicle, office automation equipment and precision machinery industries, however, the plant installed large and medium-sized indirect extruders in 1985 and 1992 to meet growing needs for high precision, high performance, and high strength extrusions. Additionally, to reduce man-hours for customers, the plant has started to provide prefabricated products, bending, cutting or drilling extrusions in-house. The Extrusion Plant is committed to stay ahead of others to develop and manufacture distinctive products.
- Production items
Aluminum and aluminum alloy extrusions (for two-wheeled and four-wheeled vehicles, electric machine parts, transportation vehicles, construction, and other general uses)
Aluminum tubes, seamless tubes and rods (extruded and drawn materials)
Aluminum extrusion materials and prefabricated products - Equipment and capacity
Extrusions: 4,500 t/year
Tubes and rods: 12,000 t/year
One direct single-screw extruder
Two indirect twin-screw extruders
Kambara Capacitor Foil Plant
The Kambara Capacitor Foil Plant is a joint enterprise between Nippon Light Metal Co., Ltd. and Japan Capacitor Industrial Co., Ltd., (JCC), one of the leading manufacturers of anodized foils for electric capacitors. Electric capacitors enjoy extensive use in a variety of fields, such as digital home electronics, computers, and other electronics products, as well as in the automotive industry. The manufacture of anodized foils for electric capacitors involves chemical processing, in which the foil after the etching process is coated by a voltage-resistant film by anodization. The Kambara Capacitor Foil Plant is focused on chemical processing for high voltage resistance, where future market expansion is particularly expected. Combining JCC's processing technologies for anodized foil for electric capacitors and the Nippon Light Metal's manufacturing and surface treatment technologies for high purity aluminum, the Kambara Capacitor Foil Plant will continue to pursue unlimited possibilities taking advantage of low-cost power.
- Production items or lines of business
Anode foil for electric capacitors - Equipment and capacity
15 million m2/year
The Kambara Heat-Exchanger Plant of Nikkeikin Aluminum for Mobility Co., Ltd.
Since the start of operations in 1988 as NIKKEI HEAT EXCHANGER CO., LTD., the Kambara Plant Heat-Exchanger Section of Nikkeikin Aluminum for Mobility Company, Ltd. has supplied aluminum heat exchangers for automobiles, industrial equipment, and other applications.
In October 2023, the company, renamed Nikkeikin Aluminum for Mobility Company, Ltd., was formed to provide one-stop development, design, and production services, and in addition to the aluminum brazing technology that the company has cultivated since the start of its operations, it will apply a variety of bonding and processing technologies to create innovative products and values, thereby contributing to a sustainable society.
- Production items or lines of business
Parallel flow condensers for car air conditioners, and battery cooling plates and power devices for environmentally friendly cars - Equipment and capacity
1.5 million units/year
Nocolok brazing furnaces
Airtightness and pressure resistance testing machines
Kambara Chemical Plant
Starting operation in 1951, the Kambara Chemical Plant is the only chemical plant of Kambara Complex. Making efforts to ensure improved, stable product quality and diversify offerings to meet the ever-expanding needs of customers, the plant staff is also striving to manufacture competitive products by streamlining and automating manufacturing processes. The Kambara Chemical Plant produces caustic soda, chlorine, hydrogen, and organic and inorganic chlorine compounds. These products are used in a wide range of fields, including the aluminum, paper and pulp, water purification, agrochemical, plastics, textile, and ceramics industries. For aluminum sulfate production, Nippon Light Metal Co., Ltd. has five branch plants in the Hokkaido, Honshu, and Shikoku regions, which allows us to deliver products across the country. Focusing on the plant's proprietary chlorination technologies, the Kambara Chemical Plant will develop new products that adequately meet the requirements of customers.
- Production items or lines of business
Caustic soda, chlorine, hydrogen, chemical agents - Equipment and capacity
Caustic soda: 60,000 t/year
Chlorine: 54,200 t/year
Hydrogen: 16,800,000 m3
Ion exchange membrane electrolyzers
Manufacturing plants for inorganic chlorine compounds, such as hydrochloric acid, sodium hypochlorite, anhydrous aluminum chloride, and polyaluminum chloride
Manufacturing plants for organic chlorine compounds
The Kambara Plant Forging Product Section of Nikkeikin Aluminum for Mobility Co., Ltd.
The Kambara Plant Forging Product Section of Nikkeikin Aluminum for Mobility Company manufactures hot forging aluminum products. Hot forging aluminum products manufactured by the backward extrusion and closed forging methods cultivated by Nippon Light Metal Co., Ltd. are advantageous in that they have higher strength than casting products, help reduce weight, and are free of defects, such as blow holes. Accordingly, our hot forging aluminum products enjoy a high reputation and wide use, such as in electric parts, automotive parts, and pressure machinery parts.
The hot forging and aluminum material development technologies continue to be transferred to the Nikkeikin Aluminum for Mobility Company, contributing to a sustainable society through the creation of quality and innovative products and values.
- Production items or lines of business
Hot forging aluminum products (such as electric parts, automotive parts, and hydraulic and pneumatic machinery parts)